带绞车系统的航空发动机拆卸与安装过程仿真
约1500kg重的飞机发动机集成安装在飞机后机身位置,发动机拆卸/安装(R/I)这一至关重要的任务,往往需要以最少的人力和工具快速地完成。发动机拆装过程所用的绞车系统要求在允许的载荷范围内无干扰地平滑啮合,这一过程相应的设计变量和零件优化形状通过RecurDyn仿真得到了确定。
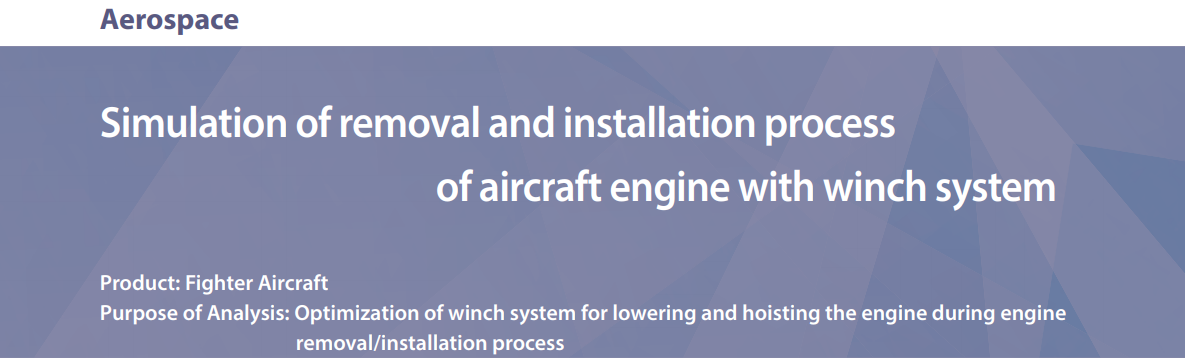
Customer Challenges 面临的挑战
- 需找到不干扰机身情况下的发动机升降系统最佳安装点
- 需要准确预测最大载荷,包括冲击载荷,以确保其在允许范围内
- 为确保安全、避免损坏,需要顺利拆卸和安装发动机
- 绞车系统包含复杂的接触关系
- 多个部件(如电缆)都存在大变形非线性行为
- 需通过大量的测试或仿真来确保实际操作条件的可靠性
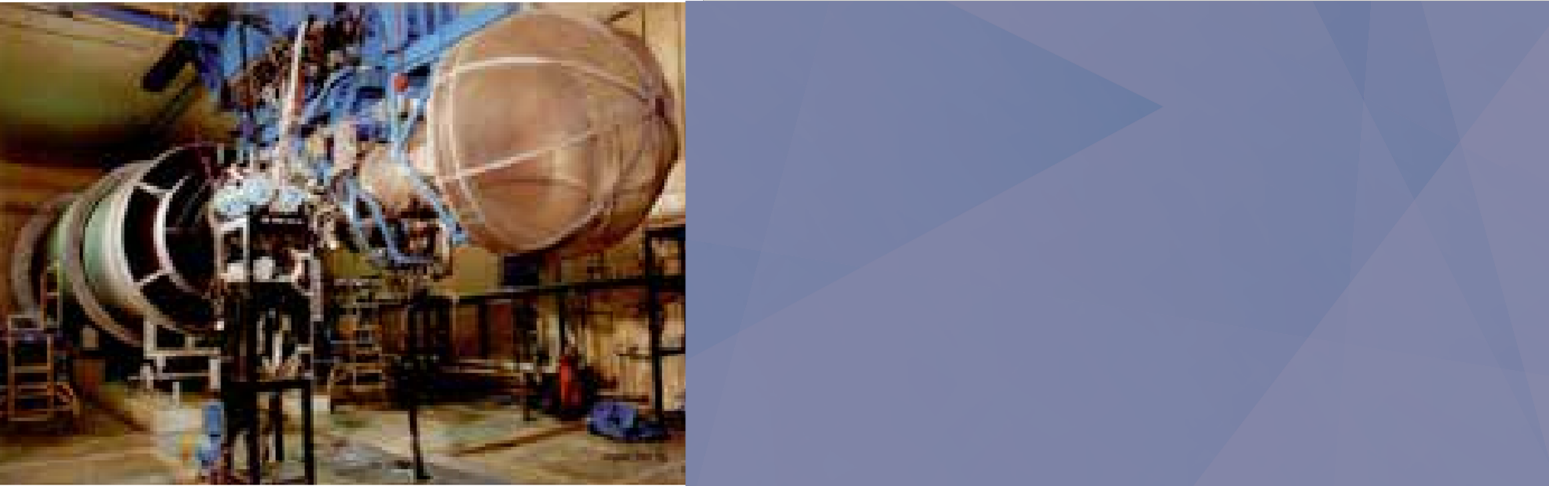
Solutions 解决方案
- 采用快速、稳健的动态求解器RecurDyn来寻找最佳设计参数,包括安装点、倾角和导轨几何形状
- 利用RecurDyn强大的接触算法进行快速准确地仿真
- 通过RecurDyn的高精度多柔体动力学模型准确预测变形、振动和载荷
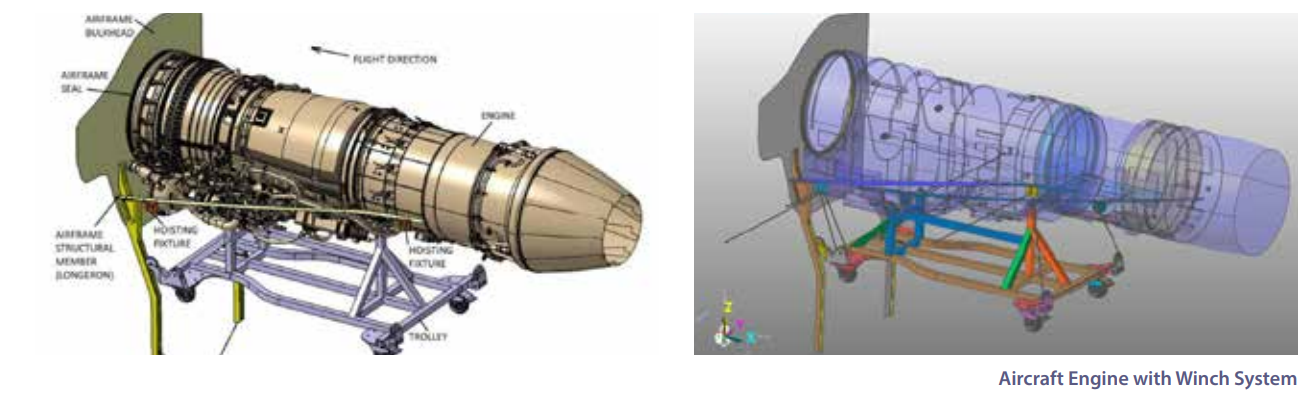
Process 流程
- 将发动机绞盘装置和发动机总成几何(CATIA模型)已导入RecurDyn
- 分别创建带导轨和不带导轨2种模型进行仿真
- 对导轨进行优化,确定理想的几何形状,减少负载,并确保发动机安装耳轴和唇式密封的平滑接合
- 找到发动机机身上绞盘钩固定装置的最佳位置
- 找到发动机上/下俯仰过程绞车缆绳的最佳前倾角
- 对两种设计方案进行比较后作出决策
Key Technologies for Analysis 关键技术
- 通过多体动力学仿真求解发动机提升机链和滑轮系统的运动
- 方便易用的刚柔接触精确求解技术
- MFBD技术正确求解运动柔性体的变形
Outcomes 效果
- 获得绞车系统的优化方案
- 通过优化,降低了导轨上的负载
- 不带导轨的绞盘机构替代方案,在现场维护中操作更简单